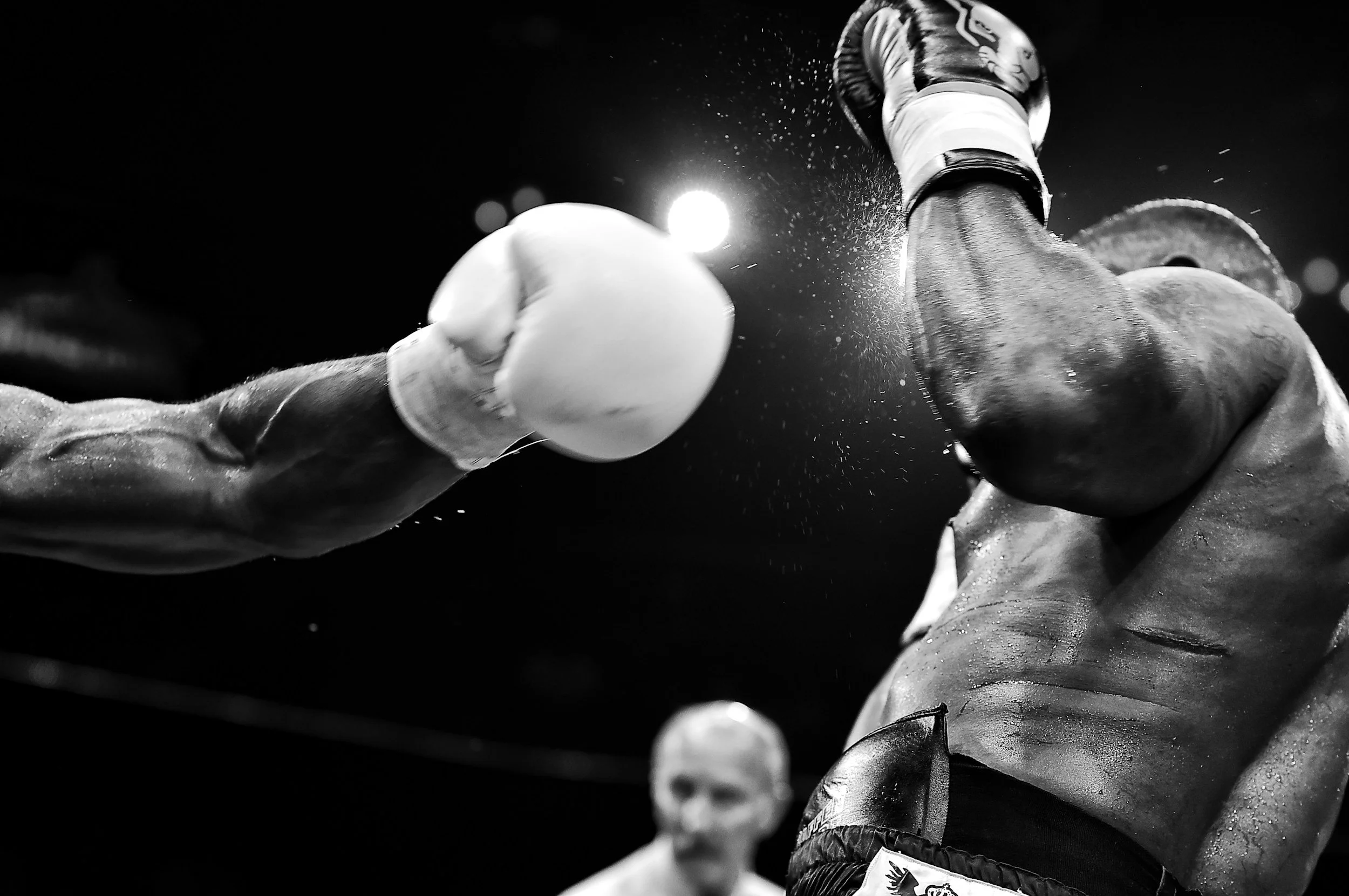
The New Workforce: how 3D can help it punch above its weight class
I’ve recently had the opportunity to speak with leaders and organizations across various industries about their operations. Workforce challenges are a recurring theme, often at the forefront of these discussions in some manner. While Kartorium’s work primarily focuses on enhancing operational efficiencies, much of it centers on supporting the people behind those operations. In deeper conversations, it's clear that many employees are going above and beyond to keep operations running smoothly, solving problems at any cost. Organizations with these "superhero" employees are beginning to recognize a heavy reliance on them—so much so that it becomes challenging to maintain standards if these key individuals leave.
And many of these valued employees are indeed leaving. The impact of "The Great Resignation" and an aging workforce is being felt across all sectors. (Check out recent US Chamber of Commerce stats on this here). While younger generations are stepping up to meet demand, a significant labor shortage remains. The reality is that organizations will have to rely on new "superheroes"—and there will be far fewer of them.
With this in mind, I wanted to share some of the implications and challenges I see with this workforce dilemma. While there's no simple solution, I want to discuss the kind of technology Kartorium uses and how, if applied correctly, it could enable a new workforce to punch above its weight class.
The reality is that organizations will have to rely on new "superheroes"—and there will be far fewer of them.
The Knowledge Gap
In physical operations, the longer you're on the job, the more you build an intuitive understanding of how things work, where potential pitfalls are, and how to troubleshoot when things go wrong. This ‘gut feeling’ doesn’t come overnight—it’s the result of years spent learning the ins and outs of a facility, operational process, or service area.
For instance, I once spoke with a facility manager who shared a costly lesson learned: every fall, leaves would fill up a specific exterior gutter, and if it wasn’t cleaned out, it would lead to water leaking into the basement. Over the years, he knew to add this to his seasonal to-do list, but it wasn’t written anywhere. If he were to leave and a new technician came in, they’d have no reason to know about this hidden hazard unless it somehow came up in handoff training. This type of implicit knowledge often goes undocumented but is crucial for avoiding unnecessary costs.
This ‘gut feeling’ doesn’t come overnight—it’s the result of years spent learning the ins and outs of a facility, operational process, or service area.
Another example is from a manufacturing facility with a high turnover rate among technicians. During the day shift, when experienced engineers are present, problems are resolved as they arise. But at night, without the seasoned crew, less experienced techs often run into issues they don’t have the expertise to fix. A simple, minor problem—one that could take just 15 minutes to solve with the right information—can escalate into a six-hour shutdown until engineers return the next morning.
I share these stories to highlight the true impact of the knowledge gap in the workplace. Traditional training covers the basics, but the most valuable knowledge often comes from years of hands-on experience—insights that aren’t written down or formally taught. New workers may have the foundational skills, but without the specific, experiential knowledge, they face a steep learning curve.
Limits of Current Knowledge Transfer Approaches
Traditional documentation—think manuals, SOPs, 2D diagrams, and PowerPoint slides—has long been the go-to for bridging the knowledge gap between new hires and experienced workers. However, these methods often fall short in capturing the dynamic, spatial, and situational context that experienced workers rely on. As a result, they don’t provide the full picture for newer employees stepping into complex industrial environments and operational processes. Without a way to see how assets interact spatially, new hires can find themselves struggling to connect theoretical instructions to actual processes on the ground.
Traditional training covers the basics, but the most valuable knowledge often comes from years of hands-on experience—insights that aren’t written down or formally taught.
3D Technology as a Practical Solution
3D visualization of an operating environment available in the web browser
To address the limitations of traditional documentation, 3D technology offers a powerful alternative that brings operational knowledge to life. With 3D visualization tools, complex physical processes can be documented spatially, capturing the full scope of an environment and making it accessible to everyone—whether they’re new hires or seasoned operators.
Imagine a visual twin of a facility: new employees could virtually explore the environment, clicking on assets to see maintenance history, troubleshooting tips, and common issues. Instead of paging through manuals or navigating 2D schematics, they interact directly with a 3D model that shows them exactly how components connect and operate within the broader system. This gives workers an intuitive, spatial understanding of the environment they’ll be operating in, making it easier to grasp complex processes.
3D documentation tools can also help capture the ‘tribal knowledge’ of experienced employees before they retire. Veteran workers can add their insights and notes about that troublesome gutter, a finicky valve, or specific seasonal maintenance tasks and store them visually and contextually, so new hires or other team members can easily locate and understand them when they need it most.
Benefits of 3D Documentation
3D documentation of physical environments and industrial processes could transform how new employees learn, adapt, and excel. Here are several impacts I see that it could have:
Accelerated Onboarding
With 3D visualizations, new employees can quickly understand complex systems. Instead of spending weeks on manuals or training sessions, they can interact with a visual twin of their workspace, exploring assets, learning processes, and even seeing maintenance histories in real-time. This interactive, visual learning is faster and more engaging, helping new hires reach competency sooner. There’s even some research showing that trainings that incorporate spatial learning lead to retention improvements of up to 64% and as much as a 48% improvement to engagement.[1]
With 3D visualization tools, complex physical processes can be documented spatially, capturing the full scope of an environment and making it accessible to everyone—whether they’re new hires or seasoned operators.
Enhanced Troubleshooting
With detailed 3D models available at their fingertips, workers can troubleshoot and solve issues more effectively. Even inexperienced technicians can reference the 3D documentation to handle minor issues and can even collaborate with their expert team members virtually to solve problems together, even when the experts aren’t on site.
Reduced Incident Exposure During Training
In industrial environments, incident occurrence is directly correlated with level of experience. According to a Travelers Insurance report, 30% of manufacturing injuries happen within an employee’s first year.[2] By frontloading a new technician’s training with site-specific spatial knowledge, they can gain familiarity with a new operating environment without needing to set foot in the industrial environment, decreasing their risk for injury while building practical know-how for their new position.
Sustaining Institutional Knowledge Over Time
3D technology allows seasoned workers to capture and store their insights in a format that’s accessible and understandable. Their knowledge is no longer confined to individual memory but institutionalized as part of an organized, visual repository accessible to now and into the future.
Vision for the Future
Example of using 3D visualizations as the backdrop to organize and access operational information and documentation
The workforce challenge is complex, and no single solution can fully address it. Fundamentally, it’s about helping the new workforce become as efficient as their predecessors as quickly as possible. Replacing expertise is difficult, and the cost of inexperience adds up. While knowledge can be documented, I believe the real issue is communication. Even with all the right information, it needs to be presented in a medium that suits the environment where it’s applied. I see 3D technology as the universal language that can help the new workforce understand, retain, and apply the expertise left behind—and contribute their own learnings for future generations.
November 13th, 2024
6 minute read